Understanding Injection Plastic Moulding: An In-Depth Exploration
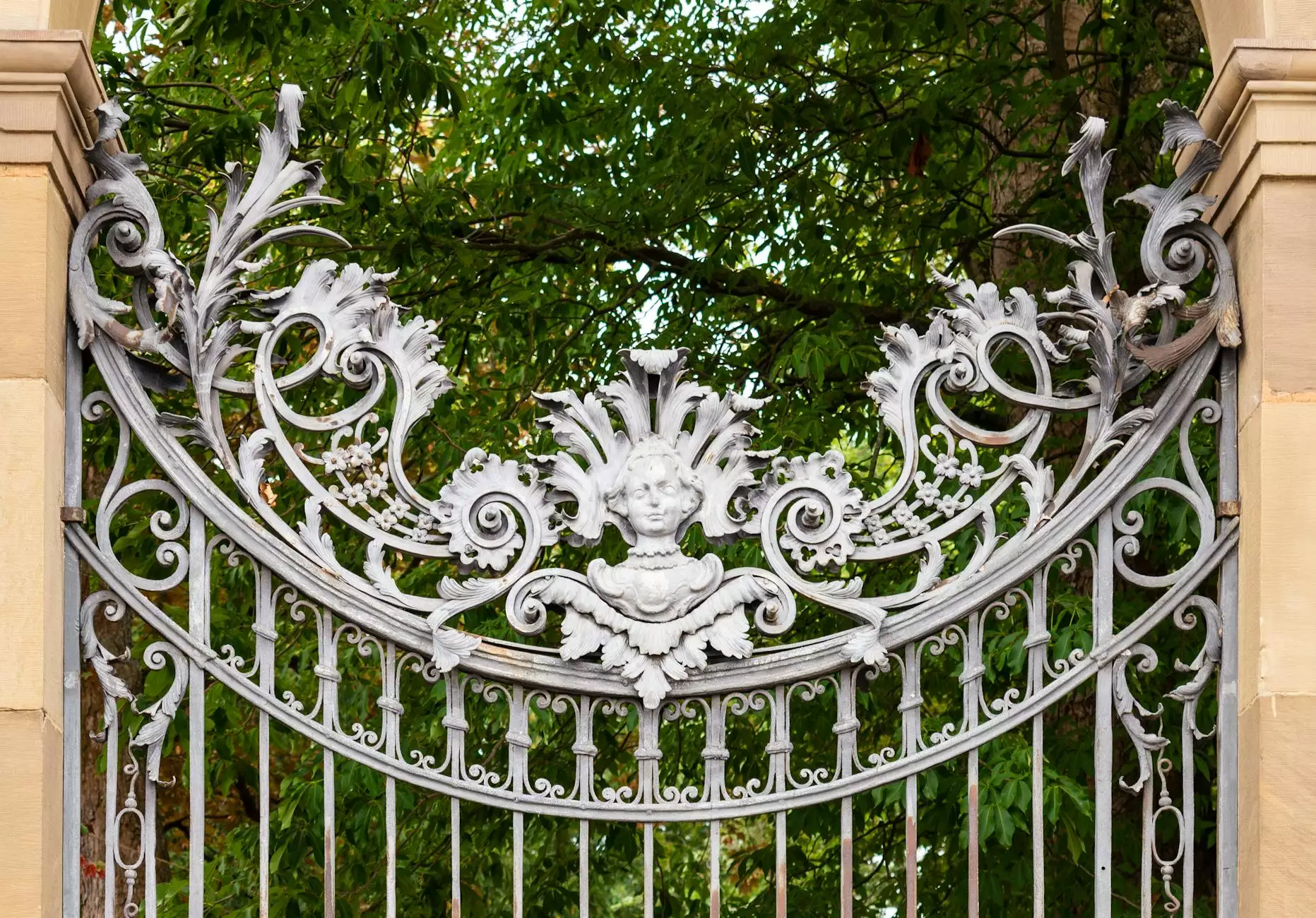
In the modern manufacturing landscape, one process that has significantly transformed production efficiency and product quality is injection plastic moulding. This innovative technique has become a cornerstone in various industries, providing unparalleled advantages in creating complex plastic components with precision and speed.
What is Injection Plastic Moulding?
Injection plastic moulding is a manufacturing process used to produce parts by injecting molten material into a mould. Typically, this material is plastic, which is melted down and injected into a pre-designed stainless steel or aluminum mould to create specific parts. The process involves several key steps:
- Material Preparation: Raw plastic materials, usually in the form of pellets, are fed into an injection moulding machine's hopper.
- Melting: The pellets are heated to their melting point, where they become a viscous liquid.
- Injection: The molten plastic is injected into a mould at high pressure.
- Cooling: The injected plastic cools and solidifies within the mould.
- Ejection: Once cooled, the mould opens, and the finished product is ejected.
The Advantages of Injection Plastic Moulding
The popularity of injection plastic moulding can be attributed to its myriad advantages, which make it a preferred choice for manufacturers across various sectors:
- High Efficiency: This process allows for the rapid production of large quantities of parts, making it ideal for mass manufacturing.
- Cost-Effective: Once the mould is created, the cost per unit decreases significantly as production scales up.
- Design Flexibility: Complex shapes and intricate designs can be easily achieved, allowing for greater creativity in product development.
- Consistent Quality: The automated nature of the injection process ensures that every part produced is uniform in terms of quality and specs.
- Material Versatility: A wide range of plastics can be used, including thermoplastics and thermosetting plastics, catering to diverse application needs.
Applications of Injection Plastic Moulding
Injection plastic moulding is utilized in a plethora of industries, reflecting its versatility and essential role in manufacturing. Some of the key applications include:
Aerospace and Automotive Industries
The automotive industry heavily relies on injection moulding for producing components like dashboards, paneling, and other interior parts. In aerospace, it's used for lightweight structural components that require durability and precision.
Consumer Goods
From household products to toys, injection moulding is pivotal in producing everyday items efficiently and at scale. Designers can experiment with shapes and sizes, resulting in innovative products that meet consumer demands.
Medical Devices
The healthcare sector leverages injection moulding for creating surgical instruments, equipment housings, and medical disposables. The consistency and cleanliness of the process are critical for ensuring product reliability and safety.
Electronics
Injection moulding is widely used for producing components such as casings, connectors, and housing for gadgets, benefiting from tight tolerances and high-quality surface finishes.
Choosing the Right Materials for Injection Moulding
The choice of material is crucial in injection plastic moulding, impacting the durability, appearance, and function of the final product. Common materials include:
- Polypropylene (PP): Known for its chemical resistance and flexible properties, it’s widely used for consumer goods.
- Polycarbonate (PC): A strong material with high impact resistance, ideal for applications requiring transparency.
- Polyvinyl Chloride (PVC): Its good chemical resistance makes it suitable for a variety of applications, particularly in construction.
- Acrylonitrile Butadiene Styrene (ABS): Popular for its rigidity and toughness, commonly used in the automotive and electronics sectors.
The Injection Moulding Process: A Step-by-Step Guide
To better understand how injection plastic moulding works, let's delve into a detailed step-by-step breakdown:
Step 1: Designing the Mould
The process begins with the design of the mould, which is crucial for determining the final product's shape and functionality. Advanced CAD (Computer-Aided Design) software is typically utilized to create precise designs.
Step 2: Constructing the Mould
The mould is crafted from high-quality metals such as steel or aluminum, ensuring durability and the capacity to withstand high pressures and temperatures.
Step 3: Setting Up the Injection Moulding Machine
Machines are adjusted based on the requirements of the production run, such as the type of plastic, injection speed, and pressure settings.
Step 4: Injecting the Material
The heated, liquefied plastic is injected into the closed mould with a significant amount of pressure, ensuring it fills all corners of the mould cavity.
Step 5: Cooling and Solidification
Once injected, the plastic must cool to set. The cooling time depends on the type of plastic and the thickness of the part.
Step 6: Ejecting the Product
Once cooled, the machine opens and ejects the final product, ready for inspection and any further finishing processes.
Challenges in Injection Plastic Moulding
While the benefits of injection plastic moulding are substantial, there are also challenges manufacturers face:
- High Initial Costs: The upfront cost for mould creation can be steep, particularly for complex designs.
- Design Limitations: Some intricate designs may not be feasible due to moulding constraints.
- Material Waste: Although the majority of the plastic is used, there can be waste during the process, especially in the cooling phase.
- Cycle Time Management: Properly managing the cycle times is essential to ensure effective production without bottlenecks.
Future Trends in Injection Plastic Moulding
The future of injection plastic moulding is poised for exciting advancements. Trends to watch for include:
1. Increased Automation
As Industry 4.0 takes hold, automation in the injection moulding process is becoming more prevalent, resulting in increased efficiency and reduced human error.
2. Sustainable Practices
With growing concerns about environmental sustainability, manufacturers are exploring biodegradable materials and recycling processes to produce eco-friendly products.
3. Advanced Materials
The development of new materials that combine the benefits of plastics with increased durability and functionality is on the rise, opening doors for more innovative product creations.
4. Customized Production
As consumer demand for personalized products grows, injection moulding technology is adapting to allow for more customizable options in the manufacturing process.
Conclusion
In conclusion, injection plastic moulding is undeniably a pivotal manufacturing process that offers numerous benefits to various industries. From its high efficiency and cost-effectiveness to its design flexibility and consistent quality, the role of injection moulding in modern manufacturing cannot be overstated. As technology advances and the demand for innovative materials and practices continues to grow, the potential for injection plastic moulding to shape the future of manufacturing is bright. By embracing these advancements and overcoming existing challenges, businesses can maintain a competitive edge while meeting consumer needs.
For companies involved in metal fabrication or those looking to incorporate injection moulding into their operations, understanding and mastering this process is essential. By partnering with experienced providers, such as those at deepmould.net, businesses can unlock the full potential of injection plastic moulding and drive innovation in their products.