Revolutionizing Industries with Custom CNC Machining
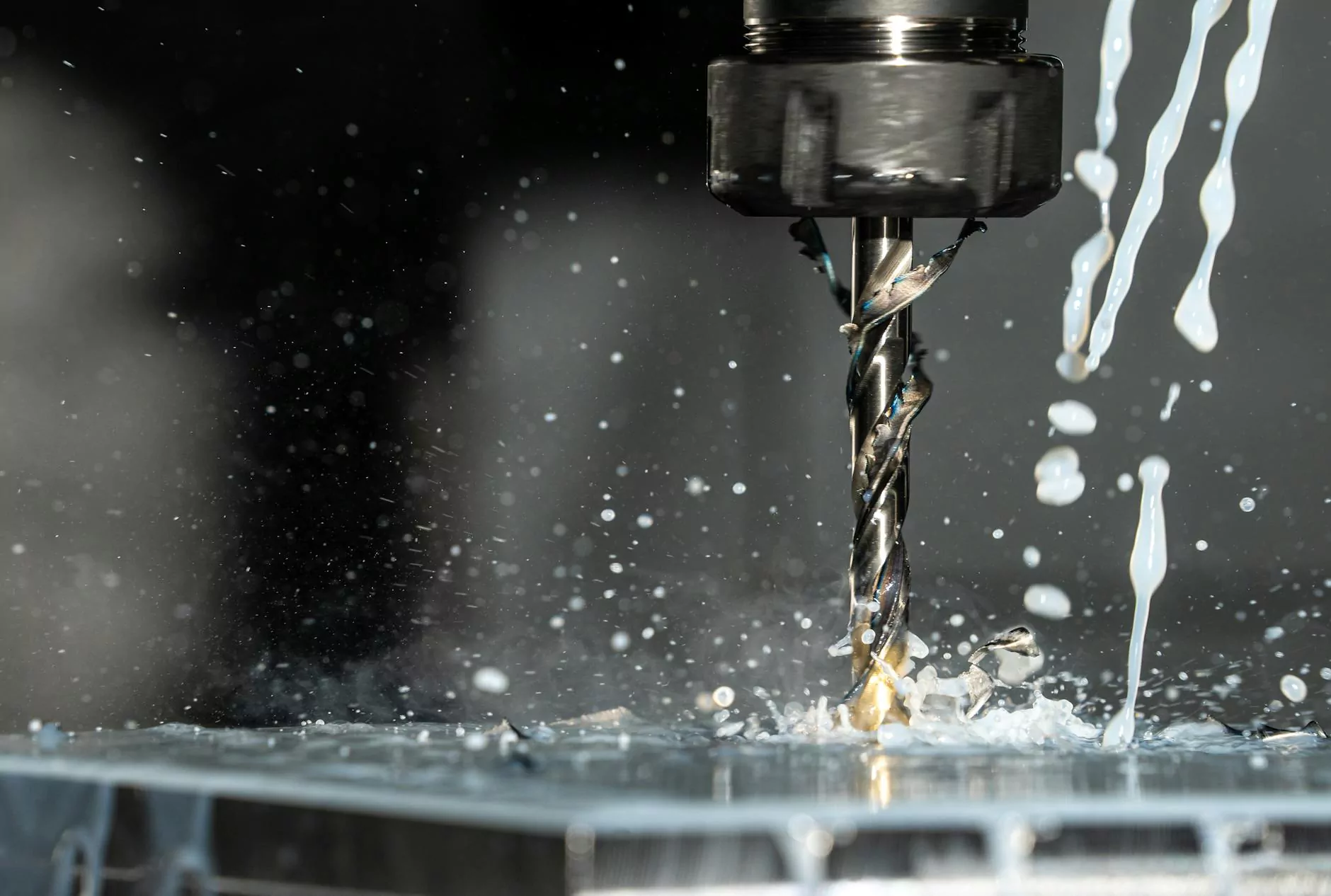
In today's fast-paced industrial landscape, custom CNC machining has emerged as a powerful tool for precision engineering. As businesses strive for efficiency and precision, the demand for advanced manufacturing techniques has soared. This article delves into the world of custom CNC machining, its benefits, applications, and how it can enhance business operations, specifically in the realm of metal fabrication.
Understanding Custom CNC Machining
Custom CNC machining, or Computer Numerical Control machining, refers to the use of computer systems to control machine tools. This technology enables manufacturers to produce intricate designs and components with unparalleled accuracy. The beauty of CNC machining lies in its ability to create complex shapes that traditional machining methods simply cannot achieve.
The Evolution of CNC Machining
Initially developed in the 1940s, CNC technology has significantly evolved. The advent of modern software and more sophisticated machinery has allowed CNC machining to be employed across various industries. Today, CNC machines can operate lathes, mills, routers, and other tools, crafting parts out of various materials such as metal, plastic, and composites.
Key Benefits of Custom CNC Machining
The advantages of adopting custom CNC machining are numerous, making it an essential process for metal fabricators and manufacturers alike.
1. Precision and Accuracy
- High Tolerance Levels: CNC machines can achieve tolerances as fine as +/- 0.001 inches, which is critical for parts that need to fit together perfectly.
- Complex Geometry: It allows for the production of complex geometries that would be impossible to create using manual machining techniques.
2. Time Efficiency
- Automated Processes: CNC machines operate continuously, reducing the time between setup and production.
- Speeding Up Production: Once the CNC program is generated, parts can be produced quickly, enabling just-in-time manufacturing.
3. Cost-Effectiveness
- Minimized Waste: CNC machining maximizes material use, significantly reducing scrap costs.
- Reduced Labor Costs: With automation, fewer operators are needed, which can lower overall labor expenses.
4. Flexibility
- Versatile Materials: CNC machining can accommodate a wide range of materials, including metals such as aluminum, steel, and titanium.
- Rapid Prototyping: Products can be tested and modified quickly, leading to faster release cycles.
Applications of Custom CNC Machining in Metal Fabrication
Custom CNC machining finds applications in various sectors, transforming how metal fabricators approach production. Here are some key areas where CNC machining is a game-changer:
Aerospace and Defense
The aerospace industry relies heavily on precision engineering. Custom CNC machining enables the production of aerospace components that must adhere to strict safety standards and tolerance specifications. From turbine parts to structural components, CNC machining ensures reliability and performance.
Automotive Industry
In the automotive sector, custom CNC machining is utilized for both prototyping and full-scale production. Components such as engine blocks, transmission housings, and suspension parts can be produced with exacting precision, leading to improved performance and lower emissions.
Medical Devices
The medical industry requires components that are not only precise but also biocompatible. CNC machining allows for the manufacturing of surgical instruments, implants, and prosthetics that meet stringent regulations while ensuring patient safety.
Electronics and Consumer Goods
In the fast-paced world of electronics, custom CNC machining plays a vital role in creating housings, casings, and intricate components that protect sensitive parts while maintaining aesthetic appeal. From smartphones to high-end audio equipment, CNC machining is pivotal.
Choosing the Right Metal Fabricator for Custom CNC Machining
With numerous companies offering CNC machining services, selecting the right metal fabricator for your needs is crucial. Here are some attributes to consider:
Experience and Expertise
Analyze the fabricator’s experience in the industry. A company that has been in business for several years will typically possess the expertise required to tackle complex machining tasks. Look for companies that have worked on projects similar to yours.
Technology and Equipment
Examine the types of CNC machines and software the company utilizes. Advanced machines that use state-of-the-art technology can produce more sophisticated designs, allowing for greater efficiency and accuracy.
Customer Service and Support
Strong customer service is a must. A good fabricator will provide significant support throughout the manufacturing process, from the initial design stage to delivering the final product. This relationship can be vital for fine-tuning projects and resolving issues.
Quality Assurance Processes
Investigate the quality control measures that the fabricator has in place. Look for companies that adhere to ISO certifications or similar standards, as this indicates a commitment to maintaining high-quality production values.
The Future of Custom CNC Machining
The future of custom CNC machining looks promising as technology continues to advance. Innovations such as artificial intelligence (AI) and machine learning are beginning to play significant roles in enhancing the capabilities of CNC machines.
AI and Automation
AI can help optimize machining processes by analyzing data in real time. This leads to predictive maintenance, reducing downtime and increasing overall efficiency. As automation becomes more sophisticated, we can expect to see the emergence of fully autonomous machining environments.
Sustainability and Green Manufacturing
Sustainability is becoming a key issue across industries, and CNC manufacturers are also focusing on eco-friendly practices. Custom CNC machining enables companies to reduce waste and energy consumption, contributing to greener manufacturing processes.
Integration with Additive Manufacturing
The integration of CNC machining with additive manufacturing (3D printing) is another exciting development. This combination can lead to the creation of parts that combine the strengths of both methods, yielding more complex structures with improved mechanical properties.
Conclusion
Custom CNC machining is revolutionizing the way businesses approach manufacturing. From its unmatched precision to its diverse applications, CNC machining is integral to several industries, including aerospace, automotive, and medical sectors.
As you consider investing in custom CNC machining services, collaborate with skilled metal fabricators who are well-versed in the technology and can help you leverage its benefits. By embracing custom CNC machining, businesses can enhance production efficiency, reduce costs, and maintain competitive advantages in today's dynamic market.
For more information about the best practices in custom CNC machining or to explore our services at DeepMould.net, we invite you to contact us and discover how we can help you achieve your manufacturing goals.